Inventory is essential for the operation of any manufacturing business, encompassing components, sub-assemblies, raw materials, semi-finished and finished products, as well as items used for repair, maintenance, and operations. Each inventory item has a distinct value that manufacturers must accurately assess by the end of the fiscal year, a process known as Inventory Valuation.
In today's dynamic and competitive marketplace, businesses are increasingly turning to enterprise resource planning (ERP) systems to streamline their inventory valuation process. ERP inventory management software provides comprehensive and integrated approaches to inventory control, allowing companies to make informed decisions and optimize inventory management strategies.
This blog will dive into the benefits, risks, methods and practical implementations of using ERP in inventory valuation management to improve efficiency and accuracy in valuation and inventory management effective.
I. Exploring Costing Methods and Their Impact on Inventory Valuation
Inventory valuation is an important aspect of financial management and business operations of companies. Accurate and effective inventory valuation offers several significant benefits:
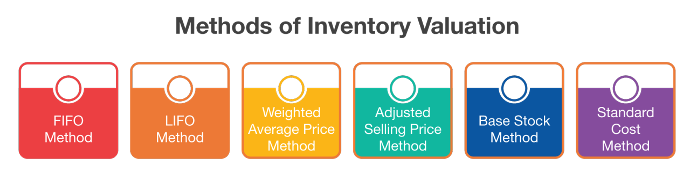
Precision in financial reporting: The way inventory is valued directly impacts profit and loss statements and the overall financial position. Ensuring accurate inventory valuation provides dependable financial data and enhances decision-making capabilities.
Effectively managing gross profit: The valuation of inventory directly impacts a company's gross profit. Utilizing appropriate valuation methods helps manage gross profit effectively and provides a clear view of the profitability potential of production and business operations.
Accurately determining product cost: The cost of goods sold is calculated based on inventory costs. Proper inventory valuation assists in determining precise cost of goods sold, supporting pricing and competitiveness in the market.
Comprehensively capturing production costs: Inventory valuation allows companies to analyze production efficiency and manage inventory cycles. Changes in inventory value can indicate whether production operations are performing well or poorly.
II. Inventory Valuation Methods
1. FIFO (First In, First Out)
Typically, manufacturers employ the FIFO (First-In, First-Out) method for inventory evaluation. This method involves selling the initial batch of products using the earliest purchased raw materials, factoring in the costs associated with these initial raw materials when calculating inventory.
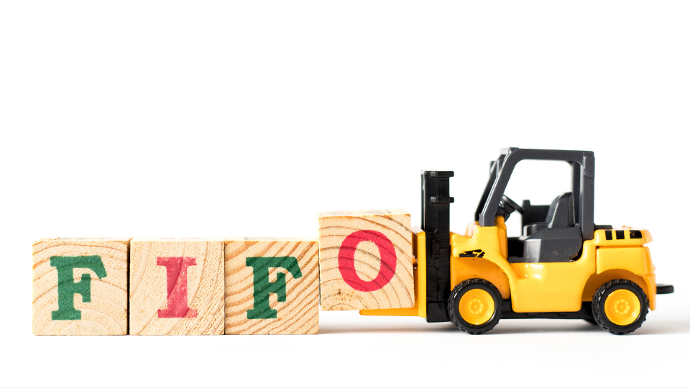
Formula to calculate cost of goods sold (COGS):
Cost of goods sold = Cost of first shipment received * Quantity of inventory sold
Formula to calculate ending inventory value:
Ending inventory value = Cost price of last lot * Inventory quantity
- Advantages: Enables quick calculation of inventory costs per shipment, providing timely data for accountants and management. This method ensures that inventory values closely align with market prices, making accounting reports more meaningful.
- Disadvantage: Results in mismatched current revenue and expenses, as revenue reflects the value of goods acquired long ago. Handling large quantities of goods through frequent import-export increases accounting costs and workload.
2. LIFO (Last In, First Out)
LIFO, as the name implies, means that the first batch of products sold comes from the most recent batch of raw materials
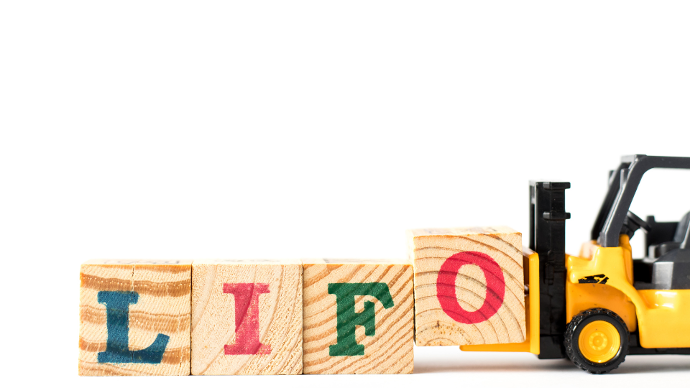
Formula to calculate cost of goods sold (COGS):
COGS = Cost of most recent shipment received * Quantity of inventory sold
Formula to calculate ending inventory value:
Value of ending inventory = Cost of first shipment * Quantity of ending inventory
- Advantages: Allows for easy adjustment of product prices permitted; Less susceptible to market price changes; Reduces capital loss from sales; Frees up additional storage space.
- Disadvantages: LIFO is applicable only to homogeneous goods with extended shelf life.
3. WAC (Weighted Average Cost)
In the WAC method, the average cost is calculated by dividing an item’s inventory cost throughout the year by the number of items.

In this method, every inventory item is tracked from the time its purchased, and stocked till its sold. This method is used in the case of larger items that are easily differentiated from each other.
III. How does ERP software assist manufacturers in achieving accurate inventory valuation?
With ERP software, manufacturers can easily select and implement appropriate inventory valuation methods to ensure accurate and timely inventory assessments. Incoming raw materials, parts, and assemblies are swiftly recorded using barcodes or RFID tags within the ERP system, capturing essential details like value, quantity, and purchase date. This data is then centralized in the ERP database for streamlined year-end valuation processes.
Manufacturers can choose their preferred valuation method, typically FIFO, at the start of the financial year within the ERP platform, ensuring consistency throughout operations. They can also assign specific valuation methods to item categories, simplifying complexity by grouping similar items together. Furthermore, modern ERP systems offer advanced costing methods such as the landed cost approach, which incorporates various expenses like production, packaging, shipping, handling, taxes, duties, and insurance to calculate a comprehensive total cost. Additionally, manufacturers can directly include service or goods costs to the original product cost within the ERP, allowing for flexibility in handling scenarios such as third-party transportation expenses without the need for a purchase order.
IV. Conclusion
Inventory holds significant importance for manufacturers, and accurately assessing its value is crucial. A deep grasp of inventory valuation and the systematic approaches to determining precise values greatly influences bookkeeping. Furthermore, understanding the true asset value sets the foundation for strategic growth and expansion plans.
SotaERP's integrated accounting and inventory modules assist manufacturers in efficiently evaluating their inventory assets.
Contact us for more information!